VI. Publicity
|
In order to create favorable attitutes toward
recycing and composting it is important to notify the public
exactly when and how yard waste will be collected. Some publicity
techniques include newspaper and radio press releases, posters,
and notices in utility bills. Good communication about collection
dates should reduce both the amount of foreign material collected
with the leaves and the inclusion of yard wastes with other solid
wastes destined for the landfill or incinator. |
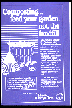 |
Signs should be posted at the entrance of the
composting facility. They should indicate the nature of the project,
facility name, operating hours, and business address and telephone
number of the operator. There should be signs that direct collection
vehicles to the unloading areas and indicate traffic circulation
patterns. If there is a drop-off site, there should be directional
signs to assist the public in locating the site and signs posting
rules for the dellivery of yard waste. |
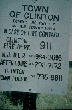 |
VII. Equipment
|
Equipment requirements for yard waste processing
vary substantially with the type and size of operation. Interlocal
agreements between neighboring towns can provide economies of
scale which may allow municipalities to buy equipment which is
capital intensive. |
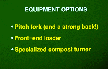 |
A front-end loader is the single essential piece
of equpment for yard waste composting, and the only equipment
used by many community operations. Bucket size ranges from 3/4
to 4 cubic yards and should be dictated by engine size and intended
use. A two part drop bucket may be useful in building very large
windrows. Prices for front-end loaders equipped with the basic
accessories range from about $50,000 to $125,000. A claw attachment
for a small loader costs about $10,000. |
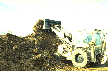 |
Windrow turners are designed especially for windrow
turning and aeration. The large models are self-propelled and
straddle the windrow. Plow fenders gather the materials into
a drum. The metal teeth on the rotating drum pick up the materials
and cast them to the teeth of the machine. The teeth shred, break
up, and aerate the compost and are aligned so that materials
are redeposited in a pyramidal windrow. Some models can be connected
to water lines so waste can be irrigated as it is turned. The
large, self-contained turners can process about 2,000 to 4,000
cubic yards per hour and cost from $100,000 top $185,000. |
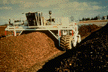 |
Smaller units are side mounted on front-end loaders
or tractors that are driven between windrows. Loader-mounted
units cost from $10,000 to $100,000. If a compost turner is to
be used, community officials may prefer to lease a turner or
share the cost with one or more other composting projects. |
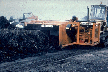 |
Screening and shredding of leaves before and/or
after composting is an optional measure. A shredder is a stationary
or trailer-mounted machine that reduces the size of the material.
It can cut composting time substantially and improve the quality
of the end product. Shredders usually have a limit of 4 to 6
inches in diameter for materials, and cost from $15,000 to $95,000
depending on size and options selected. Because a shredder is
only needed for several weeks during the year, a municipality
may want to consider renting or sharing it. |
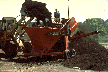 |
Screening assures a uniform size of compost.
There are a variety of screening devices that can be used in
composting operations including trommel, shaker, oscillating,
rotary and scalper screens. Units which include screens, feed
hoppers, and conveyors, range in price from $35,000 to $170,000. |
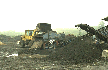 |
Chipping machines are designed bo chip brush,
limbs and other woody debris with hammers or knives. Those used
for typical municipal applications are fed by hand and have chipping
blades that range in size from 12 to 18 inches in diammeter.
Chipping machines do not separate undesirable materials from
the chips. Hand loaded commercial chippers cost from $6,000 to
$40,000. |
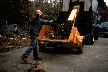 |
Tub grinders are designed to crush wood and brush that are
18 to 24 inches in diameter. They are characterized by a rotating
tub-type intake system. The rotation moves materials across a
fixed floor containing hammermills which shear the material.
As material becomes smaller, it is forced through a screen and
onto an elevator belt which discharges the ground material into
standing piles or into a transfer vehicle. Tub grinders are loaded
with a bucket loader or a conveyor belt.
Tub grinders are available in different models which have
significantly different capabilities. Grinders cost about $60,000
to $140,000 and require regular maintenance, including roation
and replacement of the hammers.
|
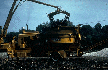 |
All material is protected by Section 107 of the 1976 copyright
law. Copyright © is held by Cornell University. If you intend
to use this material, please acknowledge its author and source.